
ADVANTAGE
Over 90% of the raw materials used in SUPERLAM are natural, with priority given to locally sourced materials to minimize imports and reduce CO₂ emissions during transportation.
We ensure these raw materials are extracted from sustainable, high-quality mines free of impurities. Additionally, the compounds used in manufacturing include a high percentage of recycled materials.
SUPERLAM is completely free of volatile organic compounds (VOCs) and does not emit VOCs under any usage conditions.
With thickness options of 3.5 and 5.6 mm, the raw material consumption is 2-3 times lower compared to similar products of traditional thickness.
The reduced thickness and weight optimize square meter transport efficiency, significantly cutting CO₂ and NOx emissions.
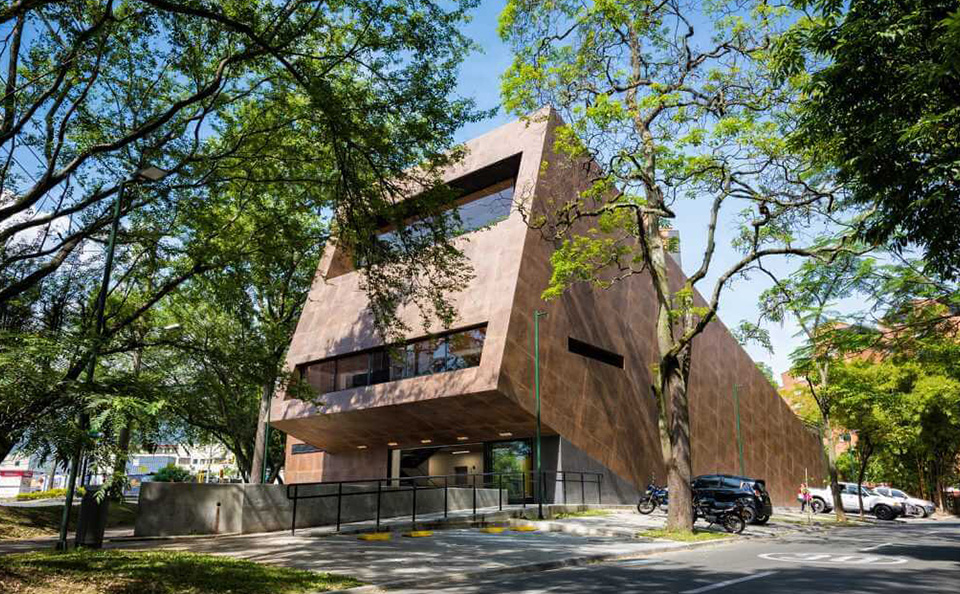
Zero Emissions
All water used in the manufacturing process is recycled internally and reused within the production plant. This ensures that no elements that could disrupt environmental balance are released externally.
Ultra-Low Crystalline Silica Content
Thanks to advanced technology, SUPERLAM has successfully reduced silica content in its composition without compromising performance.
The silica content in SUPERLAM COUNTER TOP is now less than 11%.
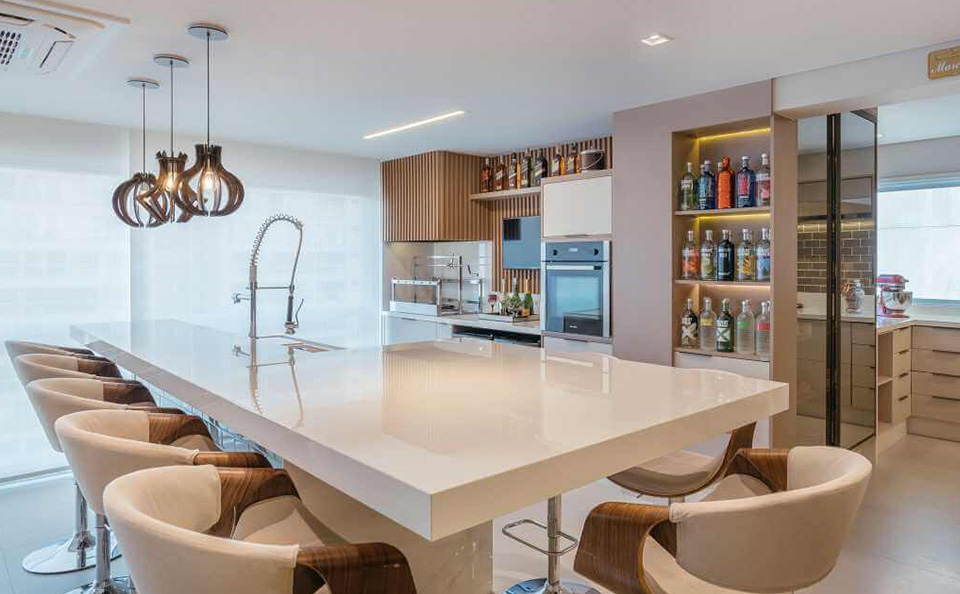
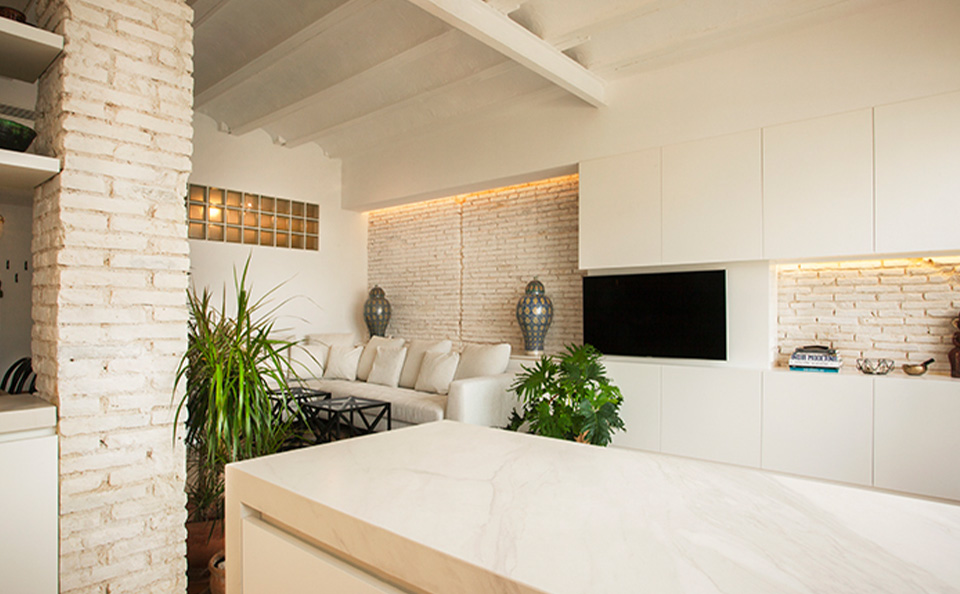
H&CTILES
The H&C Tiles treatment applied to SUPERLAM offers significant environmental benefits.
When used outdoors, it helps reduce environmental pollution and provides self-cleaning capabilities. For indoor applications, it offers antibacterial properties.
Sustainable Architecture
At SUPERLAM, we are committed to sustainable architecture. By adopting the latest LEED standards throughout the product lifecycle, from design to final installation, we help improve the energy efficiency of buildings.
Additionally, we provide documentation to meet the requirements for BREEAM, the Sustainability Assessment System for Construction Projects.
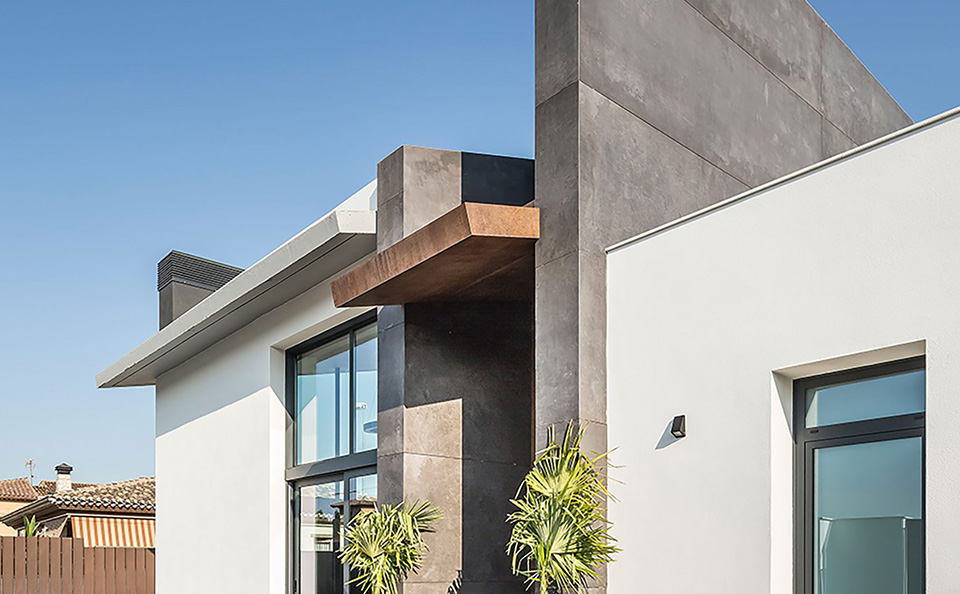
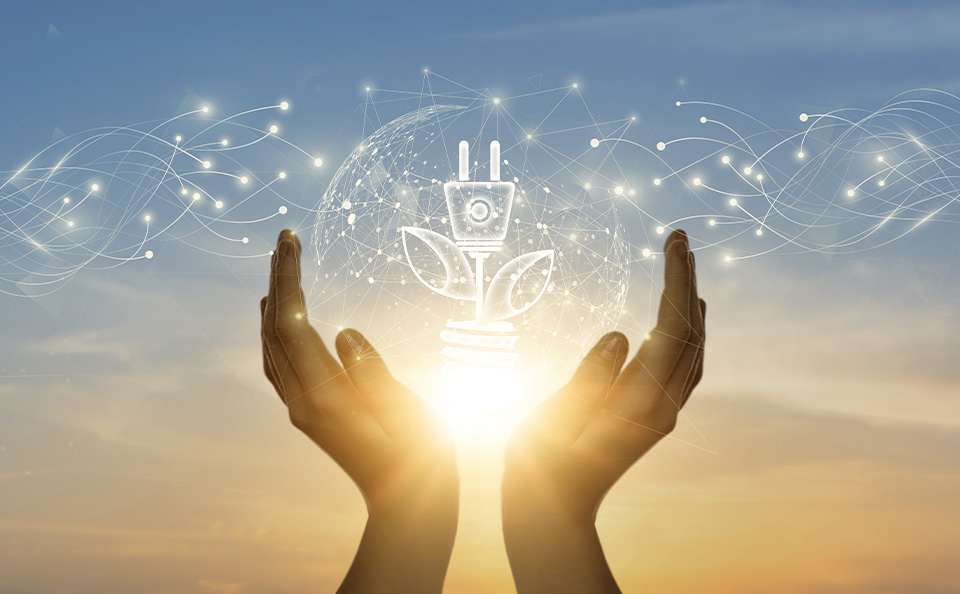
Energy Consumption with Environmental Respect
SUPERLAM follows a strategic energy plan aimed at gradually reducing consumption and implementing measures to continually lower energy use.
This is achieved through the TPM (Total Productive Maintenance) system, an integrated energy management system, and more efficient machinery that consumes less energy.